The Finned Tube Steam Air Heater for Drying is a specialized heat transfer equipment designed to efficiently convert the thermal
energy of steam into heated air, which serves as the primary drying medium. Engineered with precision, it leverages the advanced
finned tube technology to enhance heat exchange efficiency, making it an ideal choice for a wide range of drying applications
across various industries.
Products Description
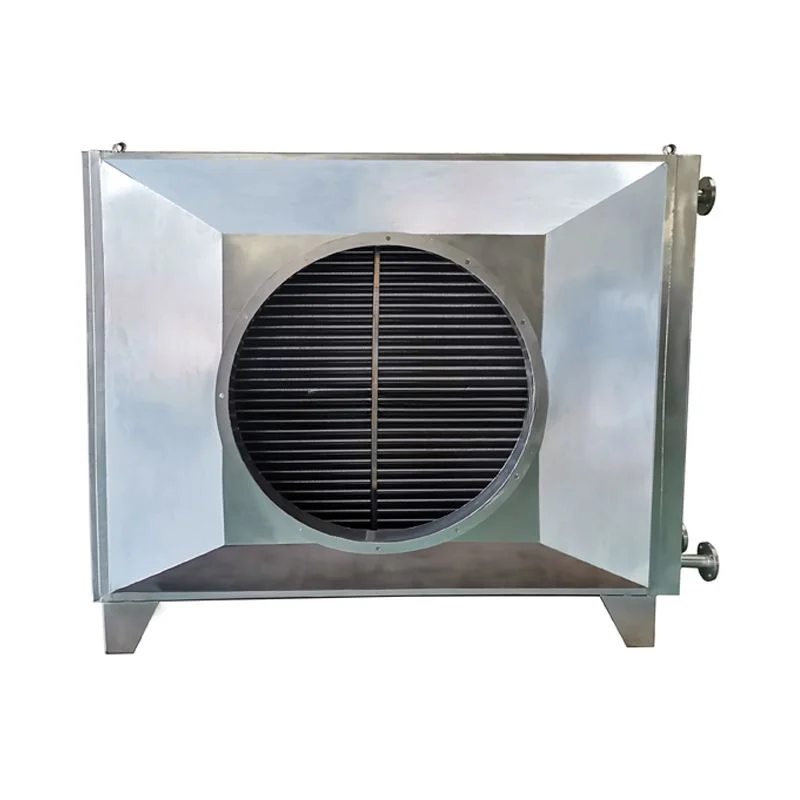
Finned Tube Steam Air Heater for Drying

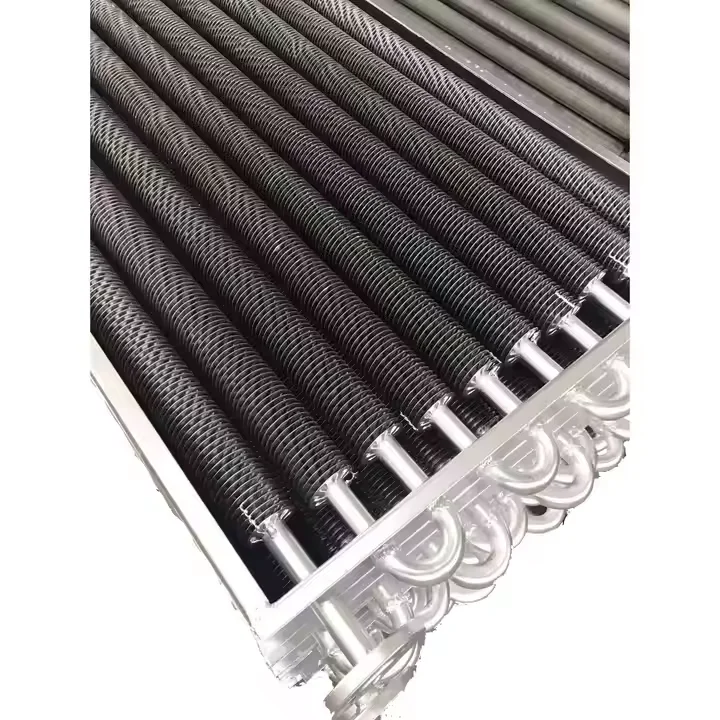
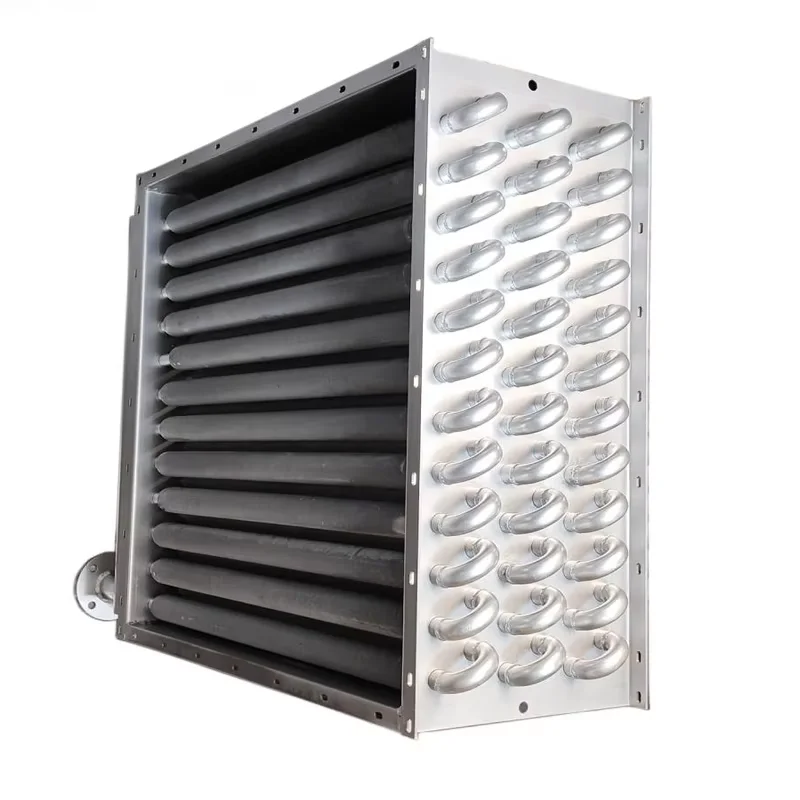
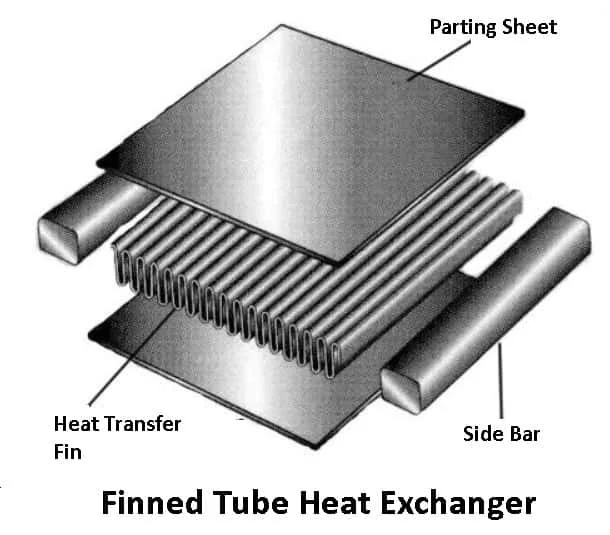
Structural Design and Working Principle
2.1 Structural Components
Finned Tubes: The core of the heater, these tubes are equipped with extended fins, typically made of high - quality metals such
as aluminum, copper, or stainless steel. The fins significantly increase the surface area in contact with the air, maximizing
heat transfer. The tube materials are selected based on the operating conditions, ensuring corrosion resistance and durability
Steam Inlet and Outlet: Strategically designed connections allow for the smooth flow of steam into and out of the heater. The
inlets are equipped with control valves to regulate steam flow, while the outlets are designed to efficiently discharge
condensed steam.
Air Duct: A well - structured air duct system guides the air flow across the finned tubes. The shape and size of the air duct
are optimized to ensure uniform air distribution and minimize pressure drop, facilitating efficient heat exchange.
2.2 Working Principle
Steam, generated from boilers or other steam sources, enters the finned tubes under pressure. As the steam flows through the
tubes, it releases its latent heat. The extended fins on the tubes quickly transfer this heat to the surrounding air. The air,
which is forced to flow across the finned tubes by fans or natural convection, absorbs the heat and increases in temperature. This
heated air is then directed to the drying equipment, where it contacts the wet materials. Through the process of convection, the
hot air transfers its heat to the materials, causing the moisture within them to evaporate and be carried away by the air flow,
thus achieving the drying process.
Finned Tubes: The core of the heater, these tubes are equipped with extended fins, typically made of high - quality metals such
as aluminum, copper, or stainless steel. The fins significantly increase the surface area in contact with the air, maximizing
heat transfer. The tube materials are selected based on the operating conditions, ensuring corrosion resistance and durability
Steam Inlet and Outlet: Strategically designed connections allow for the smooth flow of steam into and out of the heater. The
inlets are equipped with control valves to regulate steam flow, while the outlets are designed to efficiently discharge
condensed steam.
Air Duct: A well - structured air duct system guides the air flow across the finned tubes. The shape and size of the air duct
are optimized to ensure uniform air distribution and minimize pressure drop, facilitating efficient heat exchange.
2.2 Working Principle
Steam, generated from boilers or other steam sources, enters the finned tubes under pressure. As the steam flows through the
tubes, it releases its latent heat. The extended fins on the tubes quickly transfer this heat to the surrounding air. The air,
which is forced to flow across the finned tubes by fans or natural convection, absorbs the heat and increases in temperature. This
heated air is then directed to the drying equipment, where it contacts the wet materials. Through the process of convection, the
hot air transfers its heat to the materials, causing the moisture within them to evaporate and be carried away by the air flow,
thus achieving the drying process.
Key Features and Advantages
3.1 High Heat Transfer Efficiency
The finned tube design multiplies the heat transfer surface area, enabling rapid and efficient heat exchange between steam and
air. Compared to traditional heat exchangers, this heater can achieve a much higher heat transfer coefficient, reducing the
overall size and weight of the equipment while maintaining high - performance output. This results in significant energy savings
and a smaller footprint in the production facility.
3.2 Precise Temperature Control
With advanced control systems, the heater allows for precise adjustment of steam flow, pressure, and temperature. This enables
operators to accurately control the temperature of the heated air, meeting the specific requirements of different drying
processes. Whether it's gentle drying of delicate food products or high - temperature drying of industrial materials, the heater
can provide a stable and consistent heat source.
3.3 Wide Range of Applicability
Suitable for diverse industries including food processing, chemical manufacturing, woodworking, paper production, and textile
processing. In the food industry, it can be used for drying fruits, vegetables, grains, and other products without compromising
their nutritional value and flavor. In the chemical industry, it helps dry chemical powders and granules, ensuring product quality
and stability.
3.4 Energy - Saving and Environmentally Friendly
By optimizing heat transfer and reducing heat loss, the heater consumes less steam compared to conventional drying heating
equipment. This not only cuts down on energy costs but also reduces greenhouse gas emissions associated with steam generation,
contributing to a more sustainable production process.
The finned tube design multiplies the heat transfer surface area, enabling rapid and efficient heat exchange between steam and
air. Compared to traditional heat exchangers, this heater can achieve a much higher heat transfer coefficient, reducing the
overall size and weight of the equipment while maintaining high - performance output. This results in significant energy savings
and a smaller footprint in the production facility.
3.2 Precise Temperature Control
With advanced control systems, the heater allows for precise adjustment of steam flow, pressure, and temperature. This enables
operators to accurately control the temperature of the heated air, meeting the specific requirements of different drying
processes. Whether it's gentle drying of delicate food products or high - temperature drying of industrial materials, the heater
can provide a stable and consistent heat source.
3.3 Wide Range of Applicability
Suitable for diverse industries including food processing, chemical manufacturing, woodworking, paper production, and textile
processing. In the food industry, it can be used for drying fruits, vegetables, grains, and other products without compromising
their nutritional value and flavor. In the chemical industry, it helps dry chemical powders and granules, ensuring product quality
and stability.
3.4 Energy - Saving and Environmentally Friendly
By optimizing heat transfer and reducing heat loss, the heater consumes less steam compared to conventional drying heating
equipment. This not only cuts down on energy costs but also reduces greenhouse gas emissions associated with steam generation,
contributing to a more sustainable production process.
Video presentation
Customization Options
* Size and Capacity: Tailor - made to fit the available space in the production facility and meet the specific drying capacity
needs. Whether it's a small - scale production line or a large - scale industrial operation, we can design the heater with the
appropriate number of finned tubes and air duct dimensions.
* Material Selection: Based on the operating environment and the nature of the materials being dried, customers can choose from a
variety of tube and fin materials, such as stainless steel for high - corrosion environments or copper for applications
requiring high thermal conductivity.
* Control Systems: Options range from basic manual control to advanced automated control systems with PLC (Programmable Logic
Controller) and remote monitoring capabilities. This allows for seamless integration with existing production control systems
and real - time adjustment of operating parameters.
needs. Whether it's a small - scale production line or a large - scale industrial operation, we can design the heater with the
appropriate number of finned tubes and air duct dimensions.
* Material Selection: Based on the operating environment and the nature of the materials being dried, customers can choose from a
variety of tube and fin materials, such as stainless steel for high - corrosion environments or copper for applications
requiring high thermal conductivity.
* Control Systems: Options range from basic manual control to advanced automated control systems with PLC (Programmable Logic
Controller) and remote monitoring capabilities. This allows for seamless integration with existing production control systems
and real - time adjustment of operating parameters.
Manufacturing Technique
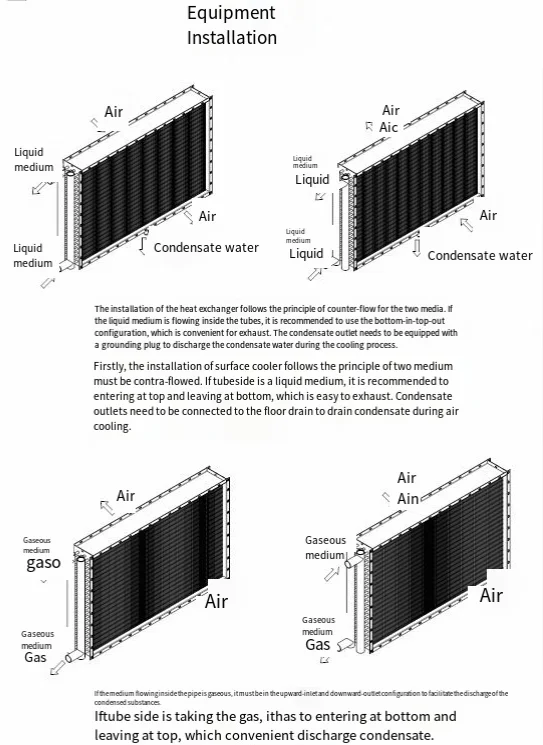
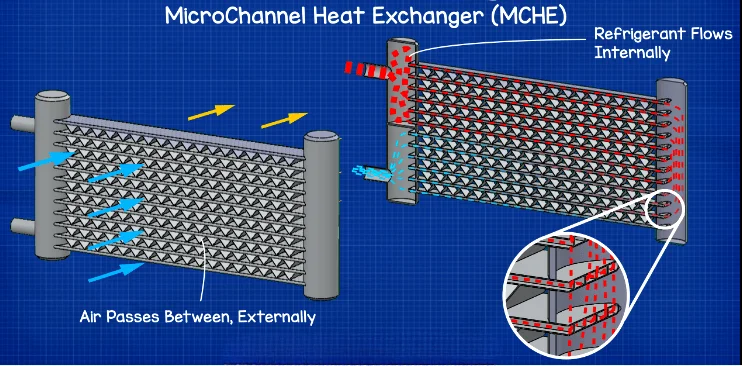
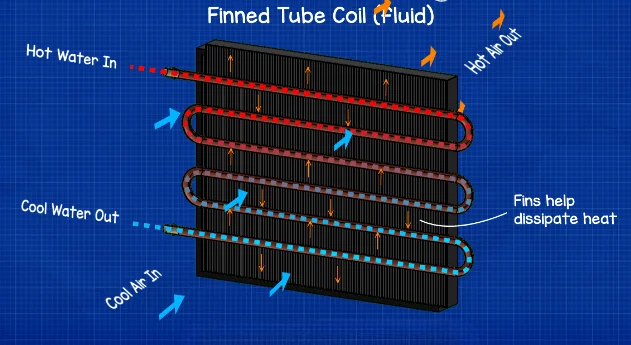
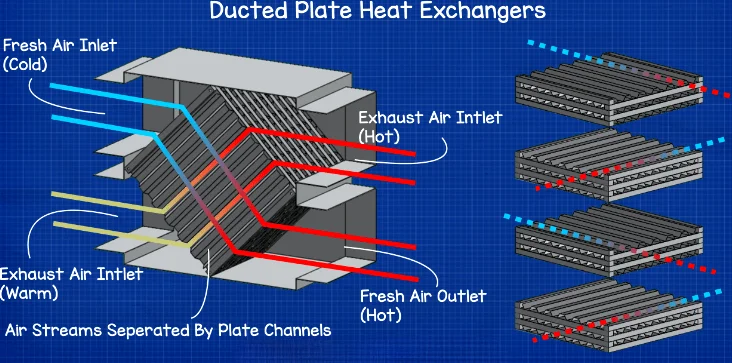
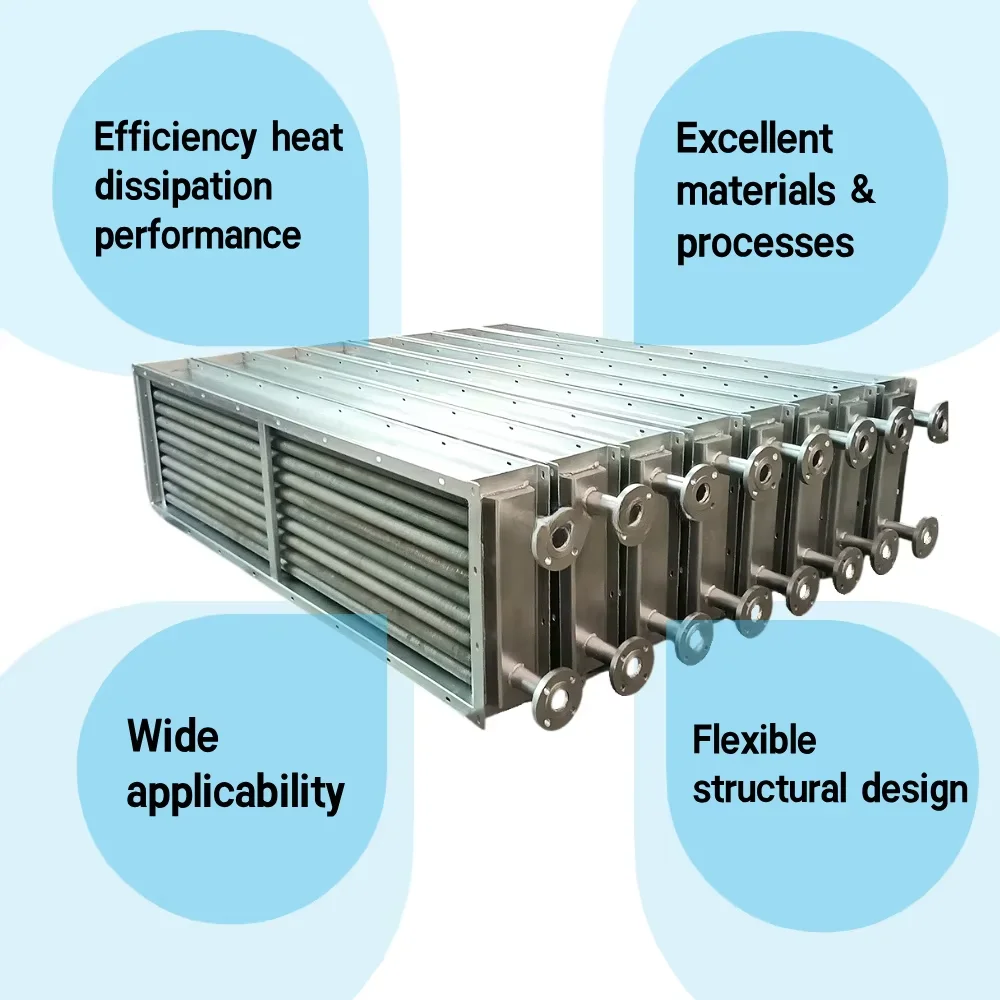
Company Profile
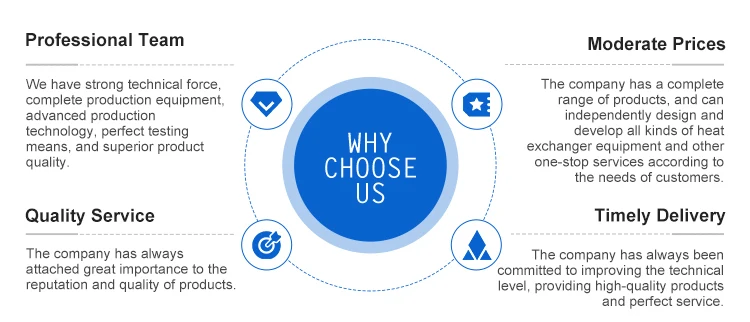
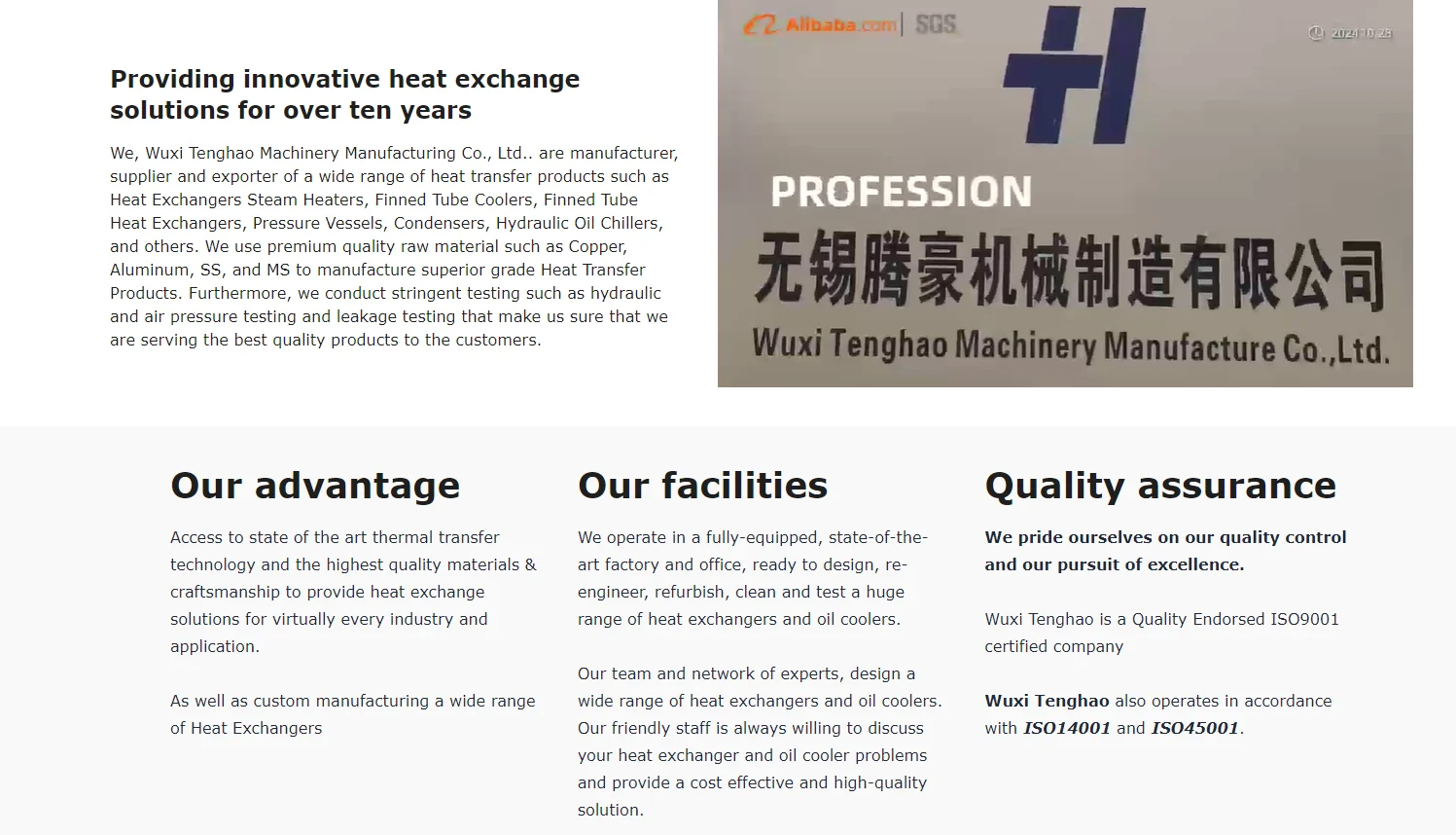
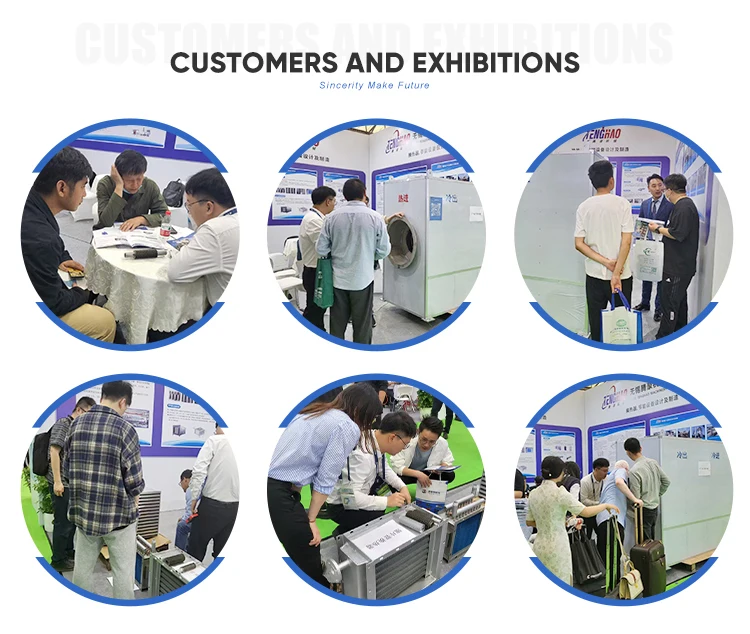
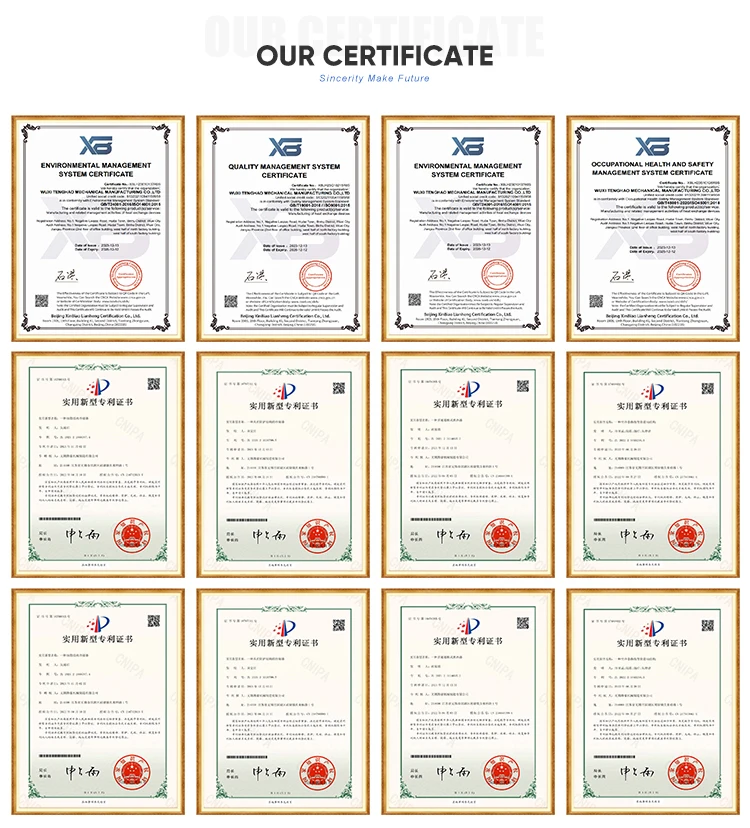
Product packaging
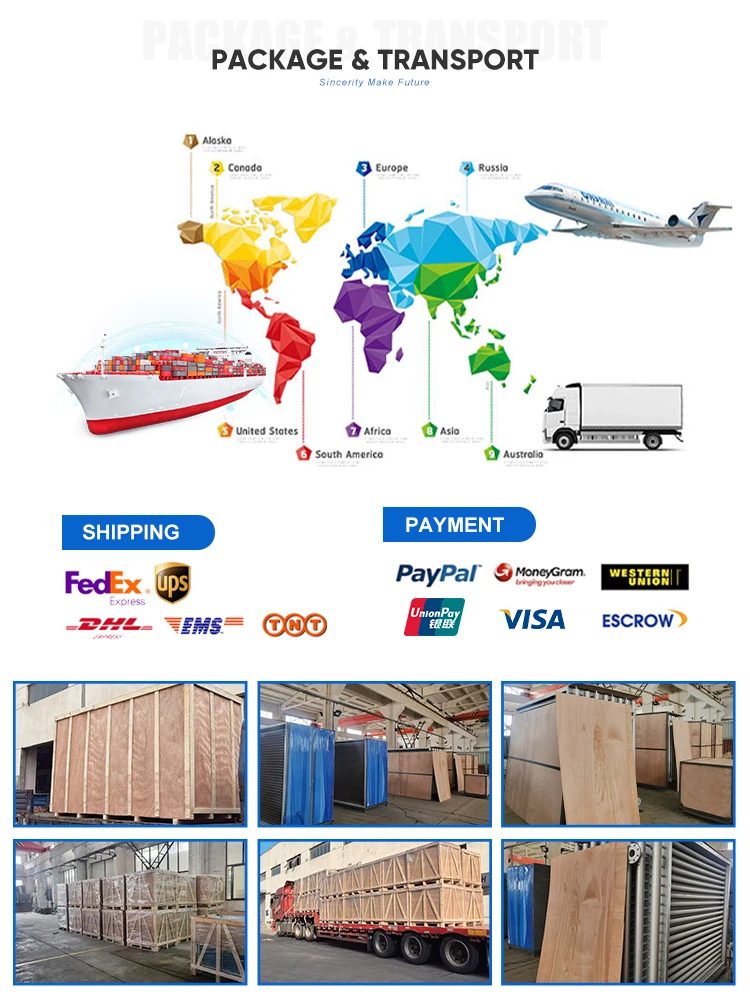
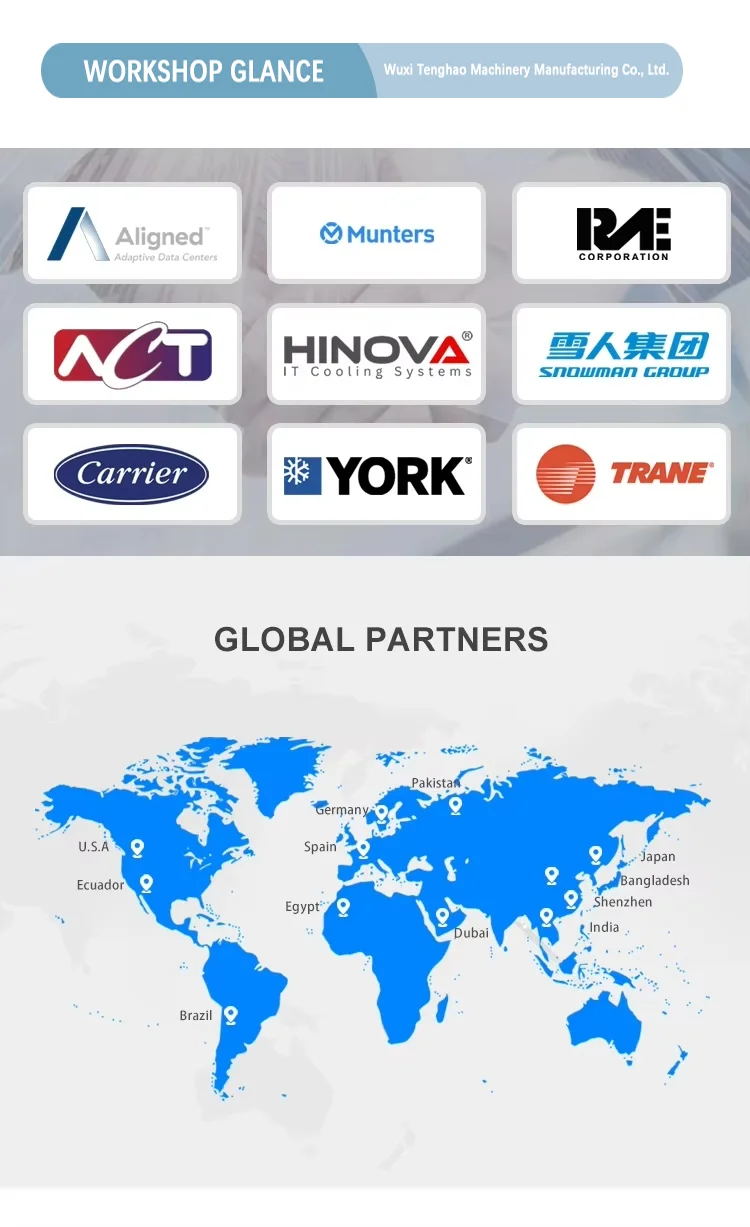
Recommend Products
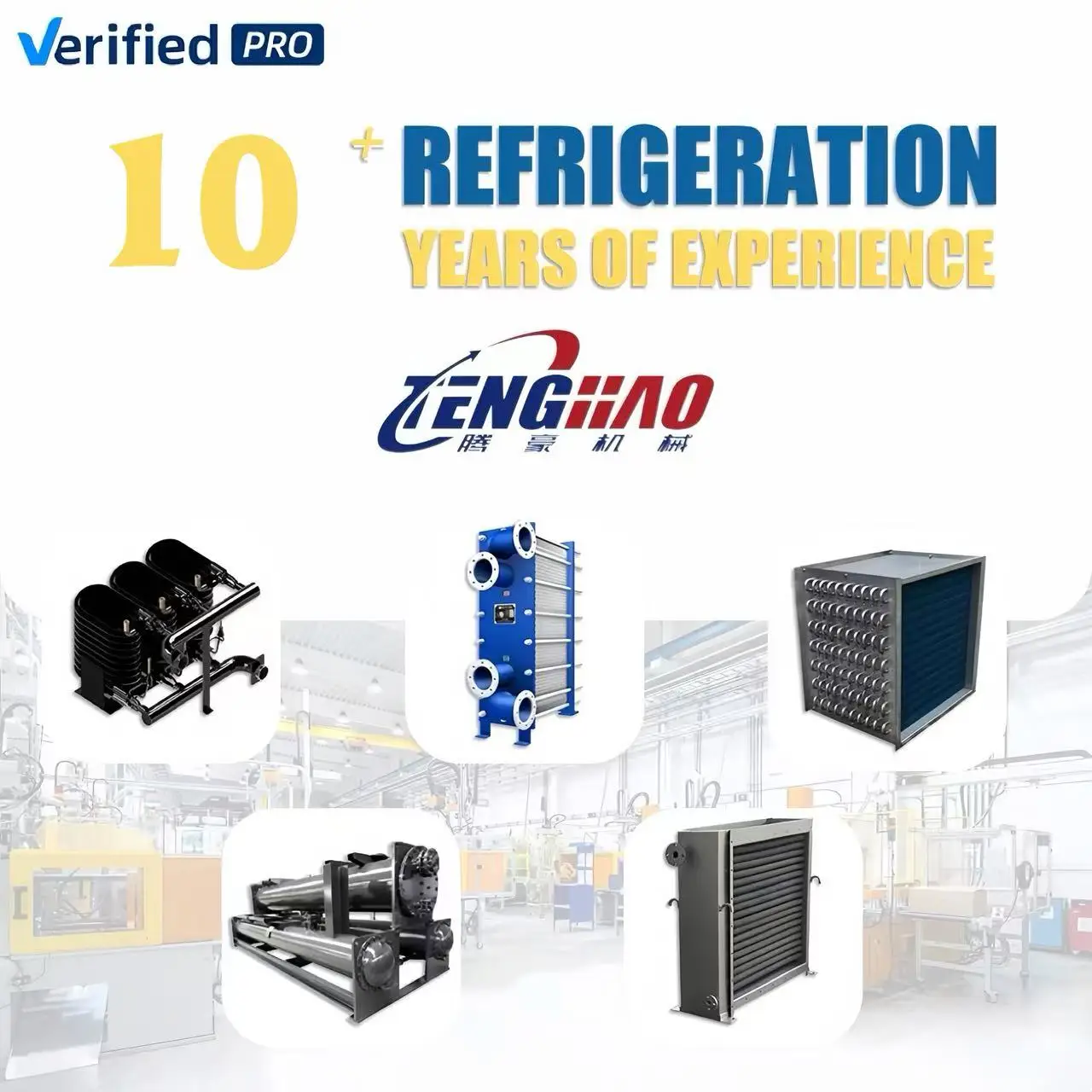
Contact information
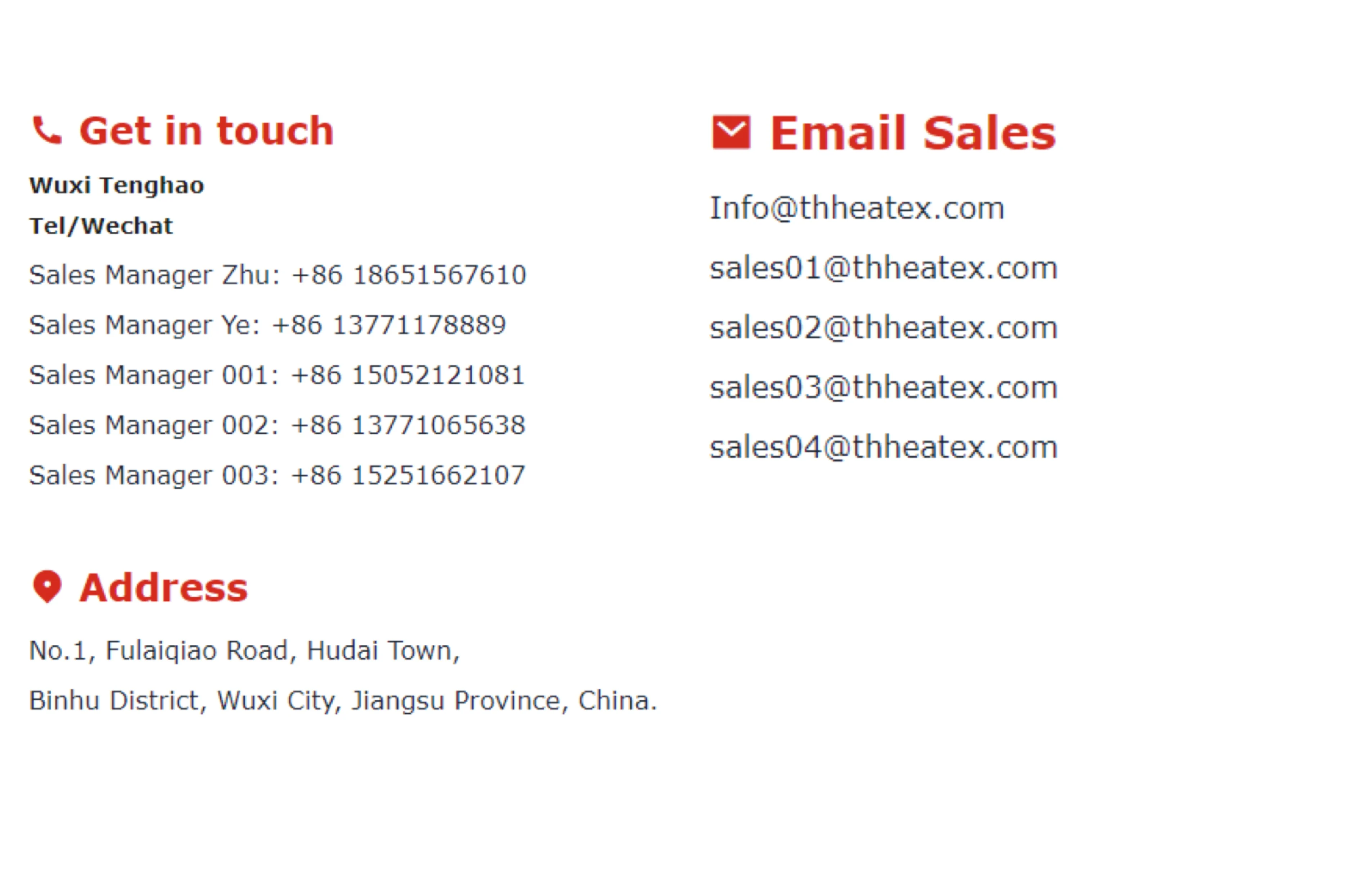
FAQ
Q:Worry about your money? A: Trade Assurance can protect your money. (more information, pls contact me) Q: Are you trading company or manufacturer ? A: We are factory.specilizing in heat exchanger for over 10 years. Q:Are your products customized? A:Yes,the products in the website are only the common type or the previous types from other customers,we can supply the newproducts according to your requirements or drawings. Q: How long is your delivery time? A: Generally it is 10-15 days if the goods are in stock. or it is 15-20 days if the goods are not in stock, it is according to quantity. Q: WHY CHOOSE US? A:We have strong technical force, with more than 10 years of experience in research and development of heat exchangers,We are committed to providing our customers with the most suitable heat transfer equipment and efficient energy saving needs.